The Definitive Guide to Designing for Additive Manufacturing Advanced Manufacturing
Table Of Content

From a product perspective, 3D printing removes many of the mainstream manufacturing limitations. Through DfAM, designers are no longer limited by the geometry or process; this allows the part or product design to be more complex, while also providing the opportunity to combine several parts into one. According to Roemer, without the setup costs of creating a new product, entrepreneurs can quickly additively manufacture objects or parts to see if they work as needed. If they don’t, they can iterate and try again, all using an additive manufacturing machine, until they find a product that does. They may not even need their own machine to do this — companies like UPS have set up 3-D printing machines at various locations that can be used by anyone.
Products and services
With additive, you have the capability to design custom fit parts with randomized lattices to help with healing and adhesion. Some of the cost hurdles that may be presented with additive manufacturing are overcome with the ability to increase functionality, specifically in medical applications. As we discussed a little in the undercuts section, you can virtually eliminate the need for subassemblies with additive technologies. You have the capability to consolidate all of your parts into one design and one production batch.
Minimum feature size
Utilizing this method, we obtained a threshold value that maximizes inter-class variance for the various features present in the acquired image. The intensities bigger than the threshold were assigned to solid and the rest were assigned to pores. Misclassified pixels encountered during this process, primarily attributed to the inherent image-related noise of XRCT, were subsequently addressed by eliminating isolated pixels as determined by connectivity. Subsequently, corresponding to the cylindrical shape of the sample, the exterior region of the sample was trimmed.
Best design software for additive manufacturing
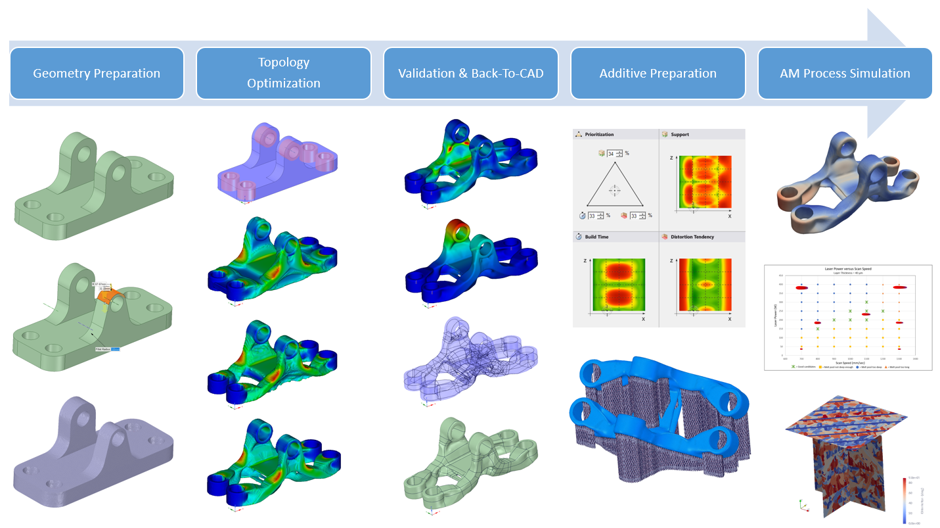
Whatever design software you use, there is one out there that is optimized and perfected for every form of additive manufacturing. When designing a very complex part, you may struggle with how to optimize your CAD software to create such designs. Many programs have become tailored or are directly compatible with additive techniques like laser sintering and 3D printing. This allows you to design your part in CAD like anytime else, then simply export your design to manufacturing.
Design for Additive Manufacturing with FDR - ENGINEERING.com
Design for Additive Manufacturing with FDR.
Posted: Fri, 12 Jan 2024 20:59:31 GMT [source]
This guide explains the basics of DfAM and introduces the intermediate and advanced concepts you need to succeed. Despite all the advantages of additive manufacturing, “I don’t see traditional manufacturing being replaced,” said Roemer. If a process involves a build plate, it can act as a support that will provide a smooth surface finish to your parts. If you stay within these parameters, you should be in fairly good shape with your design. To describe it briefly, topology optimization is the process of maximizing your material layout within the given constraints of a design. Essentially, when you use topology optimization on your part, you focus material on high-stress locations and remove material where unneeded.
Are You New to 3D Printing?
Understand the technical principles and workflows for AM of polymers, metals, and composites. Lightweight and organic-looking topology optimized automotive upright bracket designed by Lions Racing Team e.V. An interdisciplinary program that combines engineering, management, and design, leading to a master’s degree in engineering and management.
Traditional design for manufacturing and assembly (DFMA) guidelines have moulded the design transition from product concept to the final product, allowing manufacturers to produce products more efficiently and cost-effectively. In traditional manufacturing, as product complexity increases, both cost and manufacturing time also increases; thus, products are often simplified to improve manufacturability. Simplifying products, however, reduces both designer intent and often product performance. Given the size of the pores in the samples, and the overall available cross-sectional area independently of the correlation length of the sample, the size of the tube would induce a higher pressure drop than that of the sample itself.
Constraints of Traditional Manufacturing Processes
It is not a massive issue for production runs of only a few components, as the added post-processing cost is small compared to the overall design and manufacture cost. 3D printing opens the door to manufacturing more complex topologies than would be possible using traditional means. It is often feasible (and highly cost-effective) to simplify assemblies by combining multiple components into one part.
When civil engineers design a bridge, they could get the job done by building a solid block, but that would be overkill. Instead, they design the equivalent of lattices (trusses) to support the structure with as minimal material as necessary. This is similar to how latticing allows you to optimize a part and remove unnecessary material, focusing in on what is actually needed to function. Anyone can design a solid part that won’t break, but it takes an engineer to design a part that just barely won’t break.
However, the default porosity imposed by the nature of FDM was embedded without any control, and neither its connectivity nor isotropy was evaluated, even though these parameters can significantly affect the reported results. Additive manufacturing is a process of producing micromodels in a layer-like manner based on a variety of different technological approaches. The most widespread of such technologies rely on material extrusion, vat photopolymerization, material jetting, powder bed fusion, binder jetting, among many others24.
When designing overhangs, it is wise to not push the limits as large ones can cause a reduction in a part’s detail or worse, lead to the whole build crashing. Ultimately, price is based on choice of material, build time, volume of parts needed, post-processing, and more. Also, consider that strong parts can be built with minimal interior structure, saving time and money. Volume 24A provides a comprehensive review of additive manufacturing design fundamentals and applications. Tobias Ehlers is Group Leader for "Printed Effects" at the Institute for Product Development at Leibniz Universität Hannover. Current research activities are the design of dynamically loaded structural parts produced by additive manufacturing.
Research focuses on structural optimisation of particle-damped structural components and multi-material manufacturing. You may also want to focus on improving the design and functionality of a part, but given time constraints and the need of DFM, you may not get a chance. Eliminating the need for DFM in a project allows for you to focus your energy into actually improving your designs, rather than hassling with manufacturing.
Siemens Digital Industries Software helps organizations of all sizes digitally transform using software, hardware and services from the Siemens Xcelerator business platform. Siemens' software and the comprehensive digital twin enable companies to optimize their design, engineering and manufacturing processes to turn today's ideas into the sustainable products of the future. Just as additive manufacturing has revolutionized how parts and components can be made, it’s also completely changed how we should look at the design of products.
Due to this limiting factor, the experimental replicas fabricated by 3D printers typically diverge to some extent from the intended design at smaller length scales. This effect induces significant deviations between the absolute truth, meaning the natural porous medium, and the experimental and numerical results35,36. Such deviations can also have a strong influence on the printed geometries, potentially change the mechanical and overall properties of the printed sample in comparison to the actual one37,38,39. In the case of rock studies, this problem is complementary to the fact that occasionally the pore size distribution of natural rocks includes pore sizes which cannot be achieved with 3D printing, as they can be pretty small17,46,47. In recent works, the studies which were performed with binder jet technology showed a promising result in terms of resolving micro structures of natural rocks due to its inherent granular utilizing approach33,48.
Design for manufacturability is a proactive process used to maximize the design of components for the intended manufacturing process. DED is commonly used to repair or add to existing components using a multi-axis nozzle to extrude laser-melted material onto the printing surface. A powder substrate is hardened when the printing head deposits a strategically placed drop of binding fluid in a layering process. A vat of photopolymer liquid is cured by focused UV light which builds parts layer by layer without the need for structural support. This module discusses factors to keep in mind when designing projects for additive manufacturing. From a 3D-IC perspective, Siemens and TSMC successfully collaborated to certify Siemens’ Calibre® 3DSTACK solution’s support for the foundry’s latest 3Dblox standard.
To take full advantages of unique capabilities from AM processes, DfAM methods or tools are needed. Typical DfAM methods or tools includes topology optimization, design for multiscale structures (lattice or cellular structures), multi-material design, mass customization, part consolidation, and other design methods which can make use of AM-enabled features. By taking these issues into account, the necessity for validation of printed samples rises in two perspectives; (1) validation of printed geometry, (2) representativeness of the printed sample. These validations could be performed via the combination of numerical and experimental investigations with the printed samples. As it has already been shown20,21,31,33, the printed 3D geometry could be acquired by using a tomographic approach such as XRCT and/or SEM.
Comments
Post a Comment